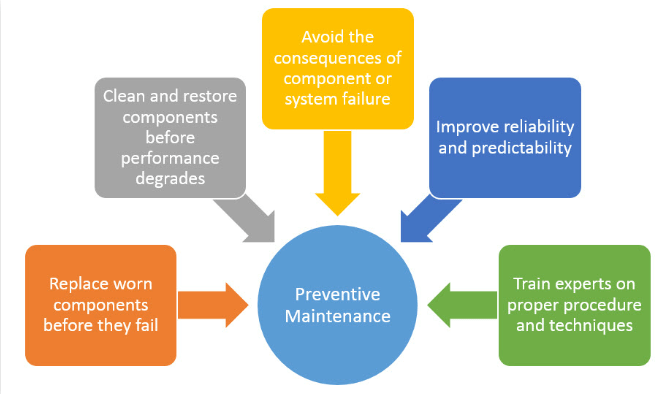
Preventive maintenance (or preventative maintenance) is maintenance that is regularly performed on a piece of equipment to lessen the likelihood of it failing. It is performed while the equipment is still working so that it does not break down unexpectedly. In terms of the complexity of this maintenance strategy, it falls between reactive (or run-to-failure) maintenance and predictive maintenance.
A successful maintenance strategy requires planning and scheduling maintenance of equipment before a problem occurs. A good preventive maintenance plan also involves keeping records of past inspections and the servicing of equipment.
Because of the complexity of maintaining a preventive maintenance schedule for a large amount of equipment, many companies use preventive maintenance software to organise their required preventive maintenance tasks.
Types of preventive maintenance
PM is used to anticipate and prevent the breakdown of equipment and should ideally be performed on all items of equipment to prevent age-related failure. Manufacturers often provide recommendations to maintain a piece of equipment but, generally speaking, there are three main types of preventive maintenance task:
Mandatory / Non-Mandatory Tasks
Mandatory tasks are those that must be performed as soon as they are due and will often include safety-critical checks. Non-mandatory tasks are still important, but can be delayed without resulting in a critical failure or performance reduction. A preventive maintenance checklist should split tasks into mandatory or non-mandatory.
Pyramiding / Non-Pyramiding Tasks
Pyramiding tasks occur when maintenance is set for a due date but is not completed and overlaps with a later scheduled maintenance. In this instance, should a new PM task become due, the previous one is cancelled. A cancellation should include a note to explain this and the new task should include the original due date to monitor how overdue the task is. Some companies prefer a non-pyramiding structure, which removes the need to note the original missed task and just takes the new date as the baseline.
Inspection and Task Oriented Tasks
Inspection tasks require checks to be made before the results are turned into work orders for planned maintenance to fix any problems that have been discovered. Task oriented PMs allow for minor repairs and adjustments to be made at the time of inspection, reducing the amount of work that needs to be written up as work orders on the inspection sheet.
Preventive maintenance can be scheduled on a time or usage based trigger. Let’s look at an example for each.
Time-based preventive maintenance
A typical example of a time-based preventive maintenance trigger is a regular inspection on a critical piece of equipment that would severely impact production in the event of a breakdown.
Usage-based preventive maintenance
Usage-based triggers fire after a certain amount of kilometres, hours, or production cycles. An example of this trigger is a motor-vehicle which might be scheduled for service every 10,000km.
Preventive maintenance planning
Planning more preventive maintenance isn’t always better. Doing PMs just to increase your planned maintenance percentage can be costly and lead to post-maintenance breakdowns.
Good preventive maintenance maintenance planning is all about fine-tuning the frequency of PMs frequencies. It’s crucial to find the right balance between doing PMs too often (expensive and risky) and not often enough (you’re likely to miss failures between inspections).
One way to done your preventive maintenance schedule is to follow the PDCA model:
- Plan: Create a baseline for PM frequencies by looking at recommended OEM guidelines, repair histories, criticality, and usage patterns for equipment
- Do: Follow your plan consistently for accurate results
- Check: Look at failure metrics for each asset to determine if your plan is working
- Act: Increase the frequency of PMs if an asset is breaking down between maintenance and reduce the frequency if you are not finding failures between PMs
Following the PDCA model and planning preventive maintenance without the help of software can be a huge challenge. Since PMs are triggered after a certain amount of time or use, it’s difficult (if not near impossible) to track that data manually, especially if you’re dealing with many pieces of critical equipment. Maintenance software allows you to set PMs according to the triggers that are appropriate for each piece of equipment. Once the trigger occurs, a work order will be created.
Maintenance software also allows organizations to gather data on preventive maintenance work orders to report on or optimize those activities, and set maintenance KPIs to work towards. AI-powered work order software takes this analysis to the next level by combing through thousands of PMs to find the ones that are leading to breakdowns, delays, and other problems so you can fix them quickly.
Advantages of preventive maintenance
Advantages compared with less complex strategies
Planning is the biggest advantage of a preventive maintenance program over less complex strategies. Unplanned, reactive maintenance has many overhead costs that can be avoided during the planning process. The cost of unplanned maintenance includes lost production, higher costs for parts and shipping, as well as time lost responding to emergencies and diagnosing faults while equipment is not working. Unplanned maintenance typically costs three to nine times more than planned maintenance. When maintenance is planned, each of these costs can be reduced. Equipment can be shut down to coincide with production downtime. Prior to the shutdown, any required parts, supplies and personnel can be gathered to minimize the time taken for a repair. These measures decrease the total cost of the maintenance. Safety is also improved because equipment breaks down less often than in less complex strategies.
Advantages compared with more complex strategies
A preventive maintenance program does not require condition-based monitoring. This eliminates the need (and cost) to conduct and interpret condition monitoring data and act on the results of that interpretation. It also eliminates the need to own and use condition monitoring equipment.
Disadvantages of preventive maintenance
Disadvantages compared with less complex strategies
Unlike reactive maintenance, preventive maintenance requires maintenance planning. This requires an investment in time and resources that is not required with less complex maintenance strategies.
Maintenance may occur too often with a preventive maintenance program. Unless, and until the maintenance frequencies are optimized for minimum maintenance, too much or too little preventive maintenance will occur.
Disadvantages compared with more complex strategies
The frequency of preventive maintenance is most likely to be too high. This frequency can be lowered, without sacrificing reliability when condition monitoring and analysis is used. The decrease in maintenance frequency is offset by the additional costs associated with conducting the condition monitoring.
The bottom line: the impact of preventive maintenance
Preventive maintenance, or PM, is regular, planned maintenance that is scheduled according to usage or time-based triggers. The purpose of PM is to lessen the likelihood of equipment breakdowns. There are many instances in which preventive is the best maintenance strategy to use, and it’s much easier to carry out a PM strategy with the help of maintenance software.
Financial and Business expert having 30+ Years of vast experience in running successful businesses and managing finance.